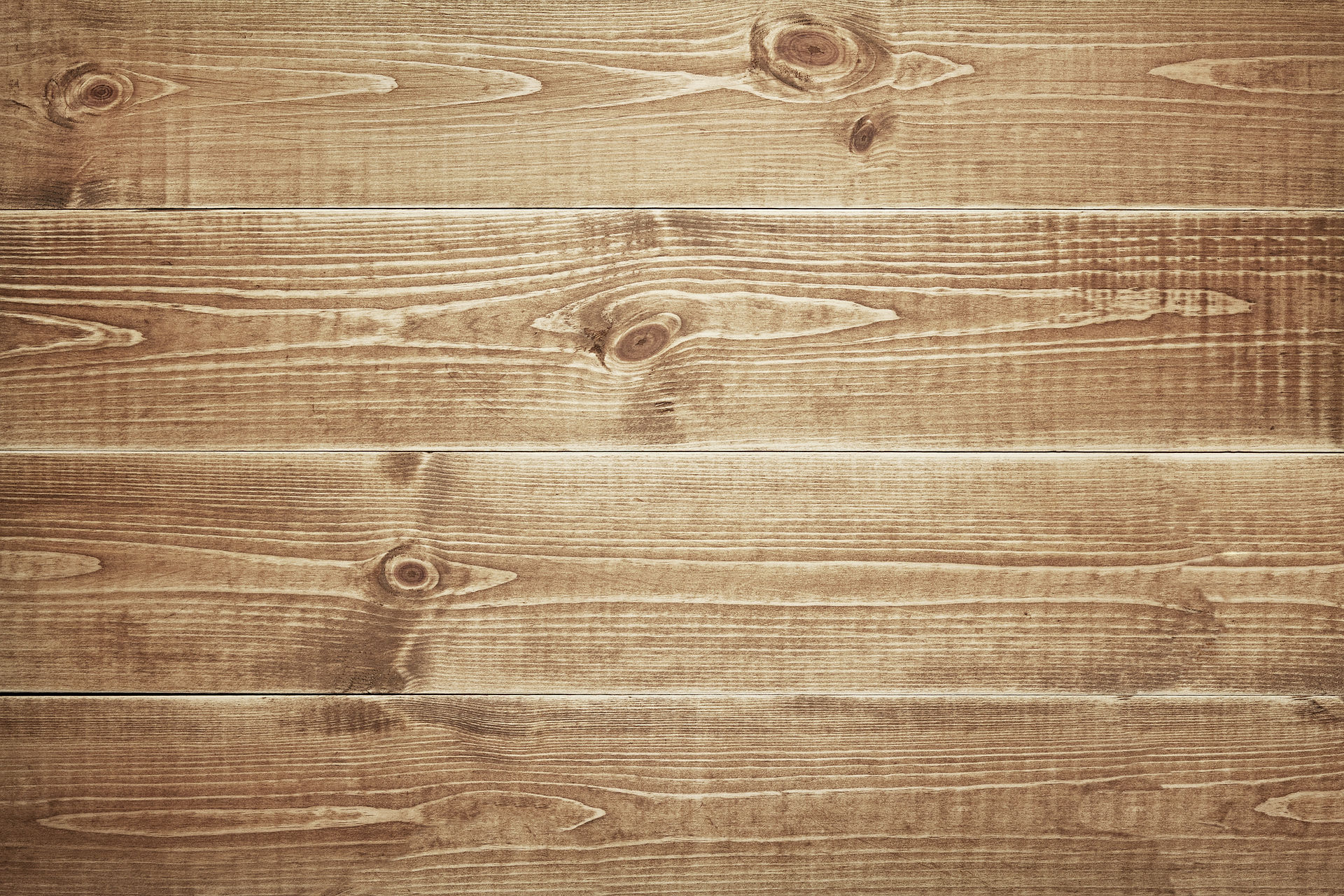
![]() Cutting | ![]() Programming |
---|---|
![]() Drilling (Step) | ![]() Drilling (Larger) |
![]() Cutting | ![]() Tacking |
![]() Adjusting | ![]() Welding |
![]() More Drilling | ![]() Reaming |
Anticipated
The most complicated issue anticipated during the construction of this device is going to be mounting the burners to the shelf arms. Since the shelf arm will be constructed from square steel tubing and the burners being used in this design have a circular support frame. This is going to require a mounting collar to be fabricated.
The center tree is going to have holes drilled through it to allow the shelf height to be adjusted to accommodate the end user. While the drilling of the holes is not a complicated process, it requires precision to ensure the spacing and centering of the holes are where they should be in order to prevent undesired stress concentrations during equipment operation.
The base hinges will be welded or bolted on after testing of each design to determine the most efficient method of ensuring a consistently square attachment. The legs must be parallel to the mating section of the base as well as flat on the supporting surface to prevent wobble of the system.
Update
The largest issue was the alignment of the pin holes and hinges for the base legs and for the shelf arms. The holes had were drilled after the tabs were welded in place due to the heat from welding moving the tabs. This method required transfer punches and step drilling, which did not allow perfect alignment of the holes. This was overcome with a tapered reamer, but it would not be ideal for mass production.
The center tree holes were done using multiple vises on the CNC mill. The collars were also done on a mill with a DRO. This method allowed for precision placement of the holes. Once all the holes were drilled, a .501 inch straight reamer was used to make sure all of the holes were perfectly aligned. The process took less time than anticipated.
The mounting of the shelf rings to the shelf arms was the easiest. Using a piece of flat bar for the rings was the cheapest option found. Due to the use of a 3-bar roller, each end of the rings, once bent, had a 2 inch flat section. This flat section mounted perfectly to the face of the shelf arms. Welding these was easily done with a simple c-clamp and vise