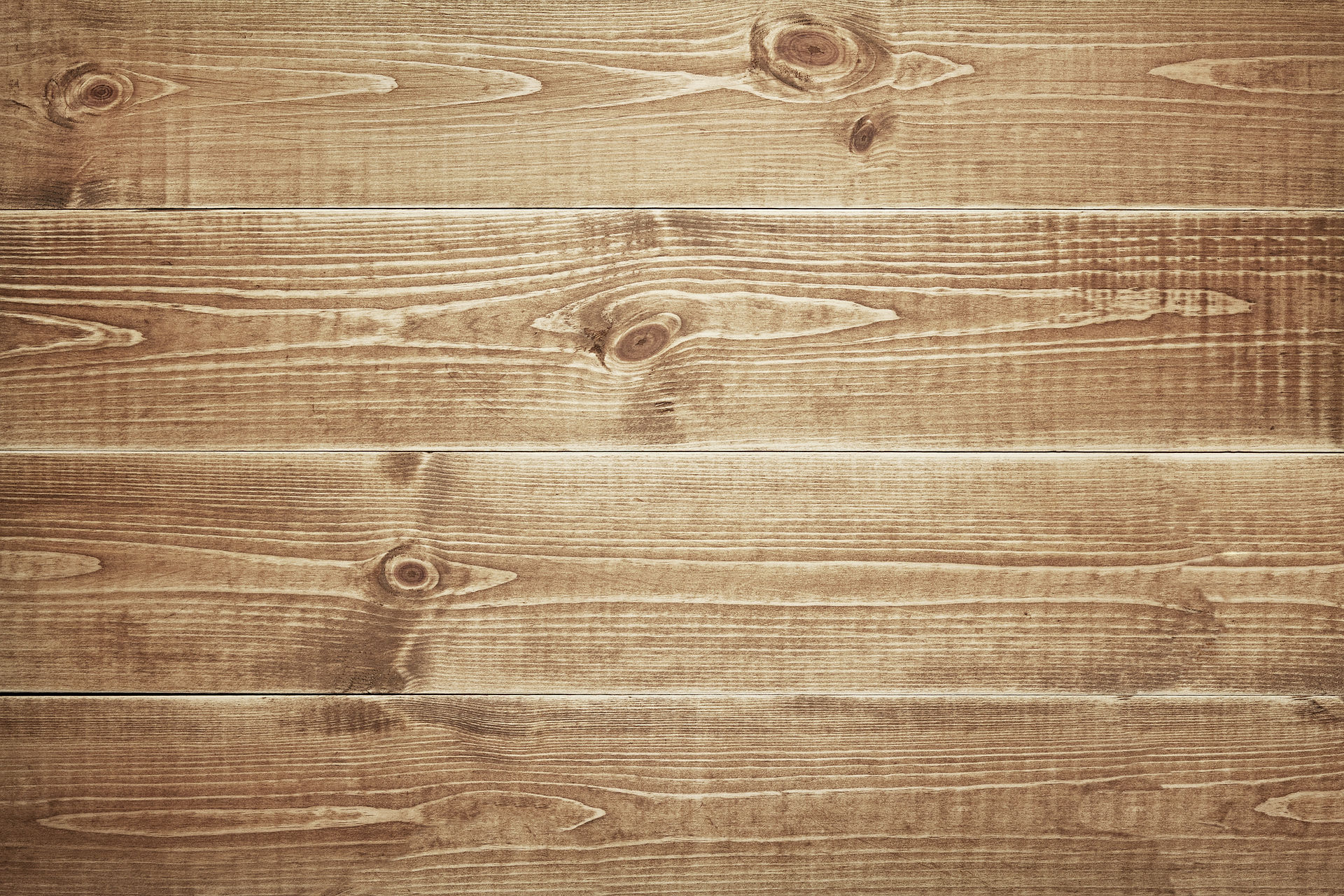
Of the eight design requirements, seven items needed to be tested to ensure success (the eighth item being the safety factor, applied to the first seven). Four of these requirements applied directly to the center tree of the rack (requirement #3, 4, 5, and 6). Requirements 3 and 5 required the most testing to ensure not only success, but safety.
Based on initial calculations and information received from the CAD designs, the following are the predicted values for the above requirements.
-
Total weight is predicted to be 89lbs based on CAD software.
-
The rack is approximately 24” x 24” x 60”.
-
The tree will flex approximately 2°.
-
Each rack is adjustable for height in 2” increments.
-
Each rack will hold over 280lbs without yielding.
-
Each rack can be mounted to any of the four sides of the tree.
-
Each rack is a minimum of 8 inches diameter.
-
The 1.2 Safety Factor will be included.
![]() Applying Strain Gauges | ![]() Applying Strain Gauges (Attempt 4) |
---|---|
![]() Calibrating Strain Gauge Software | ![]() Everything Hooked Up |
![]() Max Weight Tested | ![]() Practical Testing |
![]() Testing Under Weight and Heat | ![]() Test_1_1 |
![]() Test_1_2 | ![]() Test_1_3 |
![]() Test_2_1 |
Method/Approach
The testing of the center tree required a number of resources. The measurements and weight data were gathered through the use of shop measuring devices (tape measure, calipers, and bathroom scale). Other items required were strain gauges, Wheatstone bridge circuits, computer and strain gauge software, and calibrated weights. All of these items were available for student use at CWU. The instruction for use of the strain gauges and software was available from faculty and student lab technicians. The data from the strain gauges was able to be exported into Microsoft Excel, which was used for the angle of deflection tests as well. All graphs and other visualizations of data were completed using Excel.
The testing was all able to be accomplished in the Fluke lab without limitations. To prevent damaging the floor in case of failure, pieces of medium-density fiberboard were placed under the weights/racks.
The precision of data received for strain and angle of deflection was determined to be within 2% with the number of trials performed (3 for each test). Based on the procedures used and recommendations by industry suppliers of strain gauges, the accuracy is within 1%. No tests were within 3% of the failure envelope, therefore, all tests were given a pass without conditions. Measurement and weight data was performed 3 times each (Requirement #1, 2, 4, and 7) and averaged out. Data and graphical representations can be found in Appendix H.
Procedure for Center Tree Angle of Deflection
-
Prepare computer/notebook for recording data.
-
Measure and record each weight. Number each weight using masking tape. (The use of calibrated weights eliminates the need for this step).
-
Set up system with both racks/burner on single side ensure all locking pins are fully in place. This will determine the MAXIMUM deflection the rack could experience.
-
Place a single weight (20.0 lbs) on hot water heater to simulate water inside the pipe and heating element.
-
Place a single weight (20.0 lbs) on each burner shelf.
-
Record angle of deflection.
-
Repeat steps 5-6 until a minimum of 200lbs has been applied to each shelf (400 lbs total, 10 weights on each shelf).
-
Remove weights and repeat steps 5-7 two more times for a total of 3 sets of data.
Safety
These tests used heavy objects and high stressed steel. Closed toed shoes and eye protection were used. The devise being tested does have the risk of burns during normal operation. The removal of hot water and burning gas during testing mitigated the risk of burns.
Discussion
The testing for strain in the center tree used three different configurations to gather maximum, minimum, and most-likely stresses. With both shelves and the burner on one side (strain gauge side), the axial and bending compressive stresses were at a maximum. With all components opposite the strain gauge, the bending stress was in tension while the axial stress was in compression. With the racks and burners all on different sides, the bending stresses were counteracting one another. This configuration is the most likely to be seen during brewing, as it is the only configuration that allows a full-size brew kettle to fit on each shelf.
The testing for angle of deflection only used the maximum strain configuration to find the maximum angle of deflection. Even with both of the shelves and burner on a single side (an unusable position), the center tree only deflected a maximum of one degree.
Testing
Introduction
The testing of the Beer Brewing Rack System was completed to show success or failure for every design requirement originally listed. The testing was documented for each step to ensure repeatability for each requirement. The testing was done with the 1.2 Safety Factor for all weight requirements. All testing was done in Hogue Hall (The Fluke Lab).
The following items were listed as design requirements and were all tested.
-
It must weigh less than 150lbs total.
-
It must take up less than 2.5ft x 2.5ft x 6ft when collapsed.
-
The tree will not flex more than 2° when under a 200lb load.
-
Each rack must be individually adjustable for height in 2” increments.
-
Each rack must be capable of holding 200lbs each.
-
Each rack must be able to be mounted to any of the four sides of the tree.
-
Each rack will be a minimum of 8 inches diameter.
-
All weight requirements will include a 1.2 safety factor.